Confronting the Construction Labor Shortage: How Modular Building Can Help Bridge the Gap
Amid a nationwide housing affordability crisis, the U.S. faces another critical challenge: a severe shortage of construction workers.
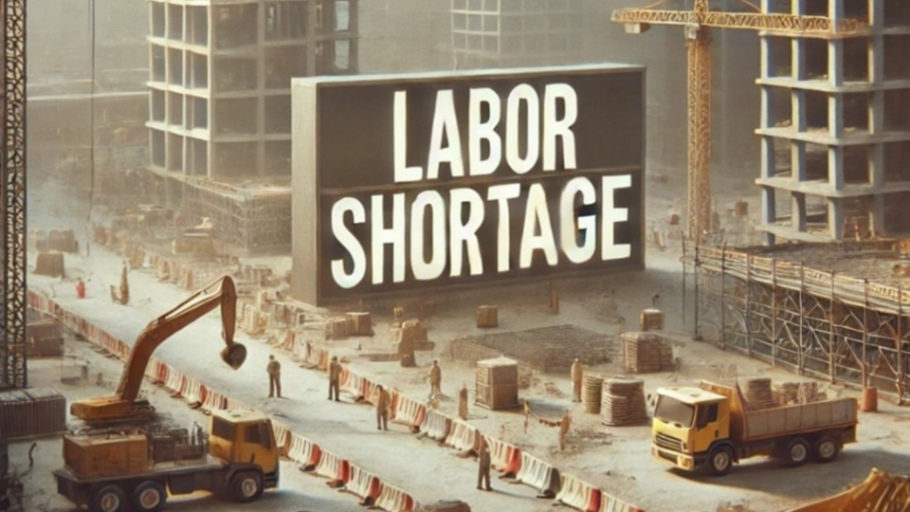
Amid a nationwide housing affordability crisis, the U.S. faces another critical challenge: a severe shortage of construction workers. Despite job growth in 2023, the construction industry still faces a shortfall of nearly half a million workers, according to the St. Louis Fed. As demand grows across various sectors—data centers, semiconductor fabs, energy, and other infrastructure projects—the labor pool for residential construction is shrinking, posing a serious threat to the future of affordable housing.
A Growing Crisis with Ripple Effects
As industries from tech to energy expand, competition for skilled construction labor will only intensify, putting further strain on the housing market. Many developers report that the demand for workers on large infrastructure projects is pulling resources away from residential construction. Without innovative solutions, this labor shortage will continue to drive up housing costs, exacerbating the affordability crisis.
The Modular Solution: Efficiency in Labor and Materials
Modular and prefabricated construction offers a promising solution. By adopting a manufacturing-based approach, modular construction can achieve significant reductions in labor requirements while still delivering high-quality results. This approach brings several key advantages:
- Reduced Labor Needs: Modular construction typically requires fewer skilled workers than traditional methods, thanks to the streamlined, assembly-line process in factory settings. This efficient use of labor can help alleviate the strain caused by the current labor shortage.
- Creation of Specialized Roles: While modular construction reduces the number of workers needed, it also creates specialized positions that draw on skills from multiple trades. This shift opens opportunities for a new generation of skilled labor, focused on quality control, assembly, and specialized manufacturing processes.
- Resource Efficiency: By centralizing the construction process, modular methods minimize material waste and allow for precise quality control. This translates into both cost and time savings, making modular construction an attractive option for developers facing high demand and tight labor markets.
Modular Construction: Not a Cure-All, but a Key Player
While modular construction may not be suitable for every project, it offers a scalable and innovative solution that can help address the labor shortage in residential construction. By adopting modular methods where feasible, the industry can adapt to changing labor dynamics and continue to build homes that meet America’s growing demand for affordable housing.
Building the Future with Modular Construction
The construction labor shortage is a complex issue with no single solution. However, modular construction represents a critical piece of the puzzle. By bringing manufacturing efficiencies to the construction sector, modular methods can help bridge the gap in labor supply, making it possible to create more housing with fewer workers. As we look to the future, embracing modular construction could be key to building a world where safe, affordable housing is accessible to all.