Traditional vs Prefab Construction
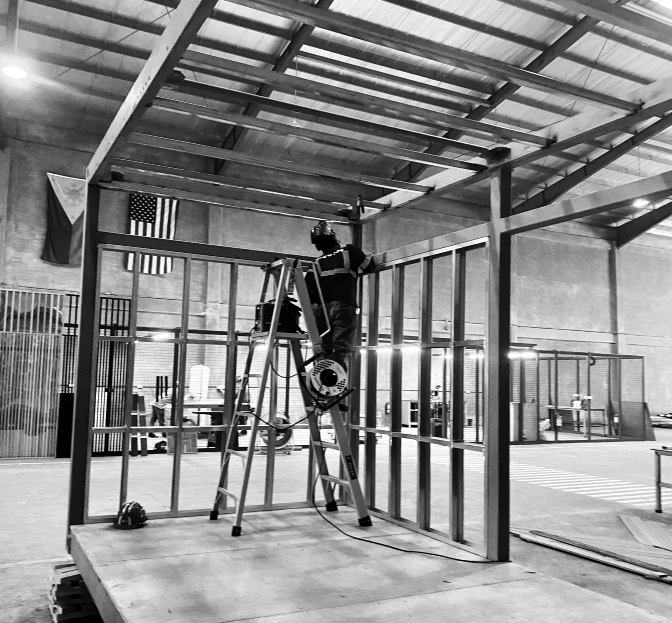
Traditional Construction
Involves building the structure on-site from the ground up, which is time-consuming and subject to delays due to weather conditions, labor availability, and site-specific challenges. This method often leads to higher costs and extended timelines.
Prefab Construction
Steel-framed, volumetric modular construction, however, leverages cutting-edge technology to fabricate entire modules in a controlled factory environment. These modules are fully finished, including electrical and plumbing systems, and are then transported to the construction site for rapid assembly. The steel framing provides enhanced strength, durability, and design flexibility, while the volumetric approach ensures precise quality control and faster completion times.
Additionally, this method significantly reduces construction waste and is more environmentally sustainable, making it a cost-effective and efficient solution for modern housing.
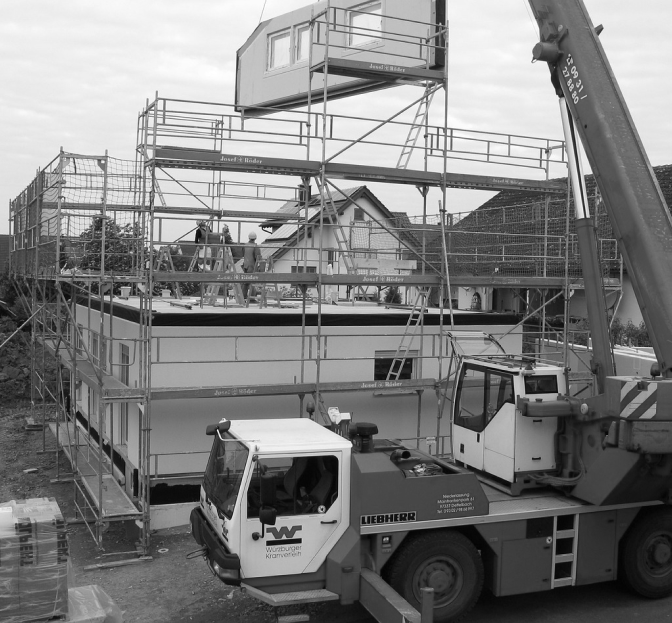